Gas Tungsten Arc Welding (GTAW): History, Process & Uses
Could the seemingly simple act of melting and joining metal be a gateway to unparalleled precision and versatility in manufacturing? Gas Tungsten Arc Welding (GTAW), often referred to as TIG (Tungsten Inert Gas) welding, has proven itself as the gold standard for achieving this, offering a level of control and adaptability unmatched by many other welding techniques.
The world of welding encompasses a diverse array of techniques, each designed to meet specific needs and material requirements. Among these, Gas Tungsten Arc Welding (GTAW) holds a particularly esteemed position. Also known as Tungsten Inert Gas (TIG) welding, this process has earned its reputation as the go-to method for applications demanding high precision and superior weld quality. It is a process that marries intricate control with versatility, enabling its use across a broad spectrum of materials and industries. This article aims to delve into the intricacies of GTAW, exploring its history, the mechanisms that make it work, its applications, and the factors that contribute to its enduring popularity.
Aspect | Details |
---|---|
Process Name | Gas Tungsten Arc Welding (GTAW) / Tungsten Inert Gas (TIG) Welding |
Synonyms | Tungsten Arc Welding, Heliarc (historical term) |
Year of Introduction (USA) | Late 1930s |
Primary Application (Initial) | Welding Aluminum Airframes |
Key Feature | High Precision, Versatility, and Quality |
Shielding Gas Used | Argon (most common), Argon/Helium mixtures |
Electrode Type | Non-consumable tungsten electrode |
Filler Metal | Often used, fed manually or automatically |
Material Compatibility | Ferrous and Non-ferrous metals, including Aluminum, Stainless Steel, and Titanium |
Process Characteristics | Manual or automated, precise control, adaptable to various positions |
Advantages | High-quality welds, Versatile, Good for thin materials, Precise Control |
Disadvantages | Slower than some other processes, Requires skilled operator, Can be more expensive |
Reference Website | Miller Electric Mfg. LLC |
The evolution of GTAW began in the late 1930s in the United States, where it was initially developed to address the challenges of welding aluminum airframes. This era marked the beginning of its journey from a specialized technique to a widely recognized method in manufacturing. Early versions of GTAW utilized helium as the primary shielding gas, leading to the coining of the term "Heliarc." However, the process has since broadened to include argon and argon/helium mixtures, the most common shielding gases used today. The ability to produce exceptionally clean and strong welds made GTAW a transformative force in the aviation industry and beyond.
At its core, GTAW relies on the establishment of an electric arc between a non-consumable tungsten electrode and the base metal. The tungsten electrode, chosen for its high melting point, is not consumed during the welding process. An inert shielding gas, typically argon or a mixture of argon and helium, plays a critical role by enveloping the weld area. This shielding gas is passed through a gas cup, effectively protecting the weld pool and the electrode from atmospheric contamination. This protection is essential, as contaminants such as oxygen and nitrogen can severely degrade the weld's integrity, leading to porosity and embrittlement.
The process begins with the welder striking an arc, usually by touching the tungsten electrode to the base metal and then lifting it slightly. The high temperature generated by the arc melts the base metal, forming a weld pool. In most applications, a filler metal, in the form of a welding rod, is manually fed into the weld pool to add to the joint's strength and fill. The precision offered by GTAW allows welders to carefully control the heat input, which is crucial in applications involving thin materials or those requiring minimal distortion. The welder carefully manipulates the torch and filler metal (if used), employing both manual dexterity and a thorough understanding of welding parameters to achieve the desired outcome.
The selection of the appropriate power source is another important consideration. GTAW can utilize both alternating current (AC) and direct current (DC). AC is frequently preferred for welding aluminum because it helps to break up the oxide layer on the aluminum surface. DC is commonly employed for stainless steel, steel, and titanium. The electrode selection is also critical. The diameter and tip geometry of the tungsten electrode, along with the type of shielding gas, directly affect the arc's characteristics and, consequently, the weld quality. Proper selection of the electrode and shielding gas is a key factor for achieving optimal performance and desired results.
GTAW is not limited to a single application but is a versatile process that finds application in diverse industries. It is the preferred process for a myriad of industries. From aerospace to automotive, and from artistic metalwork to pipeline construction, GTAW's ability to weld a wide array of metals with high precision makes it the preferred choice. It is often used for intricate welds, where the appearance and structural integrity of the weld are critical. Examples include the welding of thin-walled tubing, high-pressure piping, and components requiring excellent corrosion resistance. Furthermore, GTAW's ability to be automated opens it up to high-production manufacturing environments.
The characteristics of GTAW offer many advantages. The high-quality welds produced by GTAW are inherently stronger and cleaner. The process enables the welding of a wide variety of metals. This makes it a valuable asset for manufacturers. GTAW's precise control over heat input means that the process can be used on thin materials. It also has the benefit of minimizing distortion. However, there are also some considerations that one must consider. One of the drawbacks of GTAW is that it's typically slower than other welding processes, such as GMAW (Gas Metal Arc Welding), and can be more time-consuming.
The process requires a skilled operator, which, as a result, can contribute to higher labor costs. The equipment needed can also be somewhat costly to purchase, especially when compared to some simpler welding methods. Despite these factors, the advantages of GTAW usually outweigh the disadvantages in many situations, especially when quality is the prime factor. The precision, versatility, and consistent results provided by GTAW have solidified its place as a crucial process in many aspects of modern manufacturing.
Throughout the history of welding, there have been various significant advancements. It started with early blacksmithing practices and advanced into the development of electric arc welding. Gas tungsten arc welding (GTAW) represents a major leap forward, establishing itself as the gold standard for welding because of its flexibility and precision. The ongoing research and development in welding technology will lead to future advancements in welding processes, expanding its use.
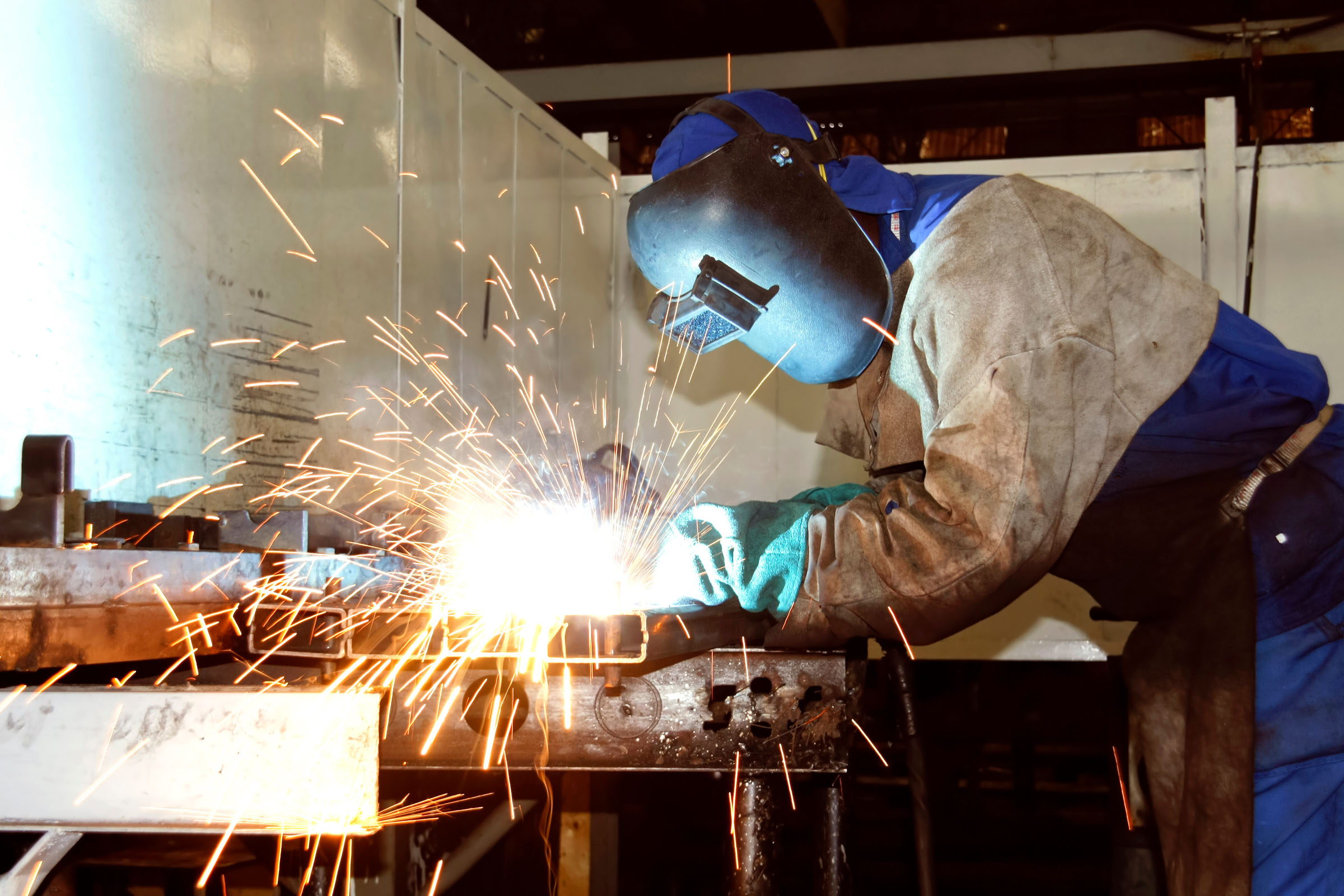
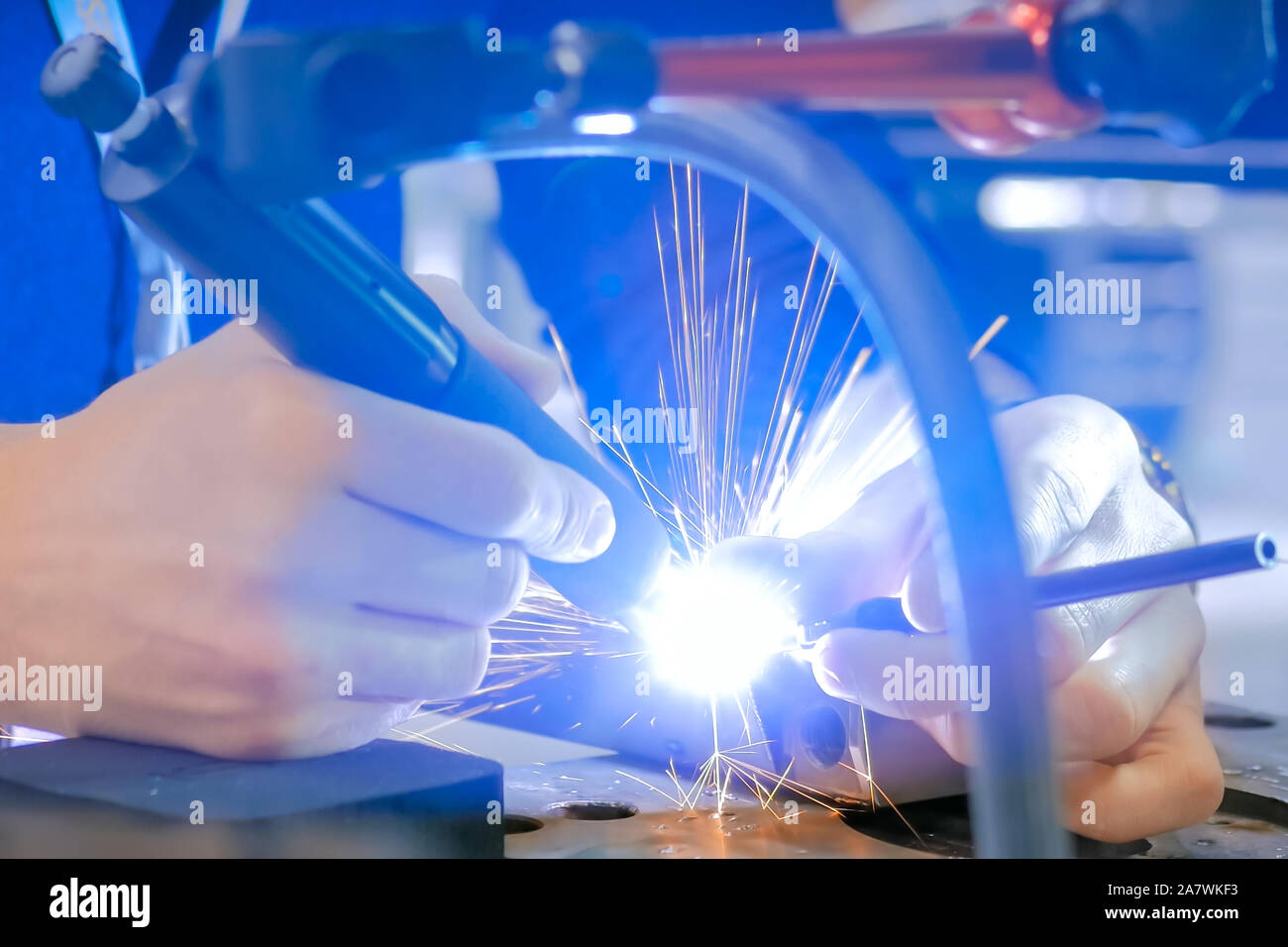
