TIG Welding (GTAW): A Comprehensive Guide To Metal Joining
Does the strength and precision of a weld truly matter when it comes to the structural integrity of critical components? Gas Tungsten Arc Welding (GTAW), often referred to as TIG welding, is celebrated for its capacity to produce exceptionally clean, strong, and precise welds, making it an indispensable process across a wide array of industries.
The world of welding encompasses a vast array of techniques, each tailored to specific materials, applications, and desired outcomes. Among these, Gas Tungsten Arc Welding (GTAW), also known as Tungsten Inert Gas (TIG) welding, stands out as a highly versatile and sophisticated method. This process utilizes a non-consumable tungsten electrode to create the weld, with the weld area protected from atmospheric contamination by an inert shielding gas, typically argon or helium. This shielding is crucial, as it prevents the molten metal from reacting with oxygen and other elements in the air, ensuring the weld's integrity and strength. GTAW is prized for its ability to produce high-quality welds, particularly on materials like aluminum, titanium, nickel alloys, and stainless steel materials that are often critical in aerospace, automotive, and other demanding fields. Its precision and control make it the go-to choice where aesthetics and structural integrity are paramount.
Consider the vast experience of Laciny Bros., a company boasting over a century of experience in metal fabrication. Their longevity is a testament to their expertise and ability to adapt to evolving industry standards. Similarly, Bolt's Metallizing, CWST, and Crooked Horn Services, operating in Texas and New Mexico, are just a few examples of businesses that have embraced the capabilities of GTAW to meet their customers' demands. Their services, ranging from residential to commercial applications, demonstrate the process's broad applicability. Darby's Welding, serving Joplin, MO, is another example, offering a variety of welding techniques that include GTAW, MIG, SMAW, and FCAW. The choice of welding method often hinges on the project's specific requirements, including the materials being joined, the desired weld characteristics, and the overall budget.
For many applications, the precision and strength offered by GTAW are simply unmatched. The ability to control the heat input precisely allows welders to work on thin materials and complex geometries, producing welds of exceptional quality and minimal distortion. This is particularly valuable when dealing with parts that are large, intricate, or difficult to fixture. The process itself involves establishing an electric arc between a non-consumable tungsten electrode and the base metal. The heat generated by this arc melts the base metal, and a filler metal, if required, is added to the weld pool. The inert shielding gas, delivered through the welding torch, envelops the weld pool, shielding it from atmospheric contaminants.
The process's sophistication is often highlighted in training programs. Organizations like Toplis Offshore Training Center (TOTC) offer comprehensive welding training programs, including courses in GTAW, designed to equip individuals with the skills and knowledge necessary to succeed in the field. Furthermore, Arc Training & Consultation Services offers its expertise by creating weld procedures and welder qualification test records for businesses to adhere to their company's standards and material needs.
TIG welding's applications are diverse, ranging from the manufacture of race car chassis to the fabrication of pipelines. Its versatility extends to both new construction and repair work. The process's ability to create clean, strong welds makes it ideally suited for industries where quality is of utmost importance. Whether it's the delicate work required in aerospace applications or the robust welds needed in construction, GTAW delivers consistent results.
The process, while highly effective, does have its own set of challenges. It often requires a skilled welder with a steady hand and a keen understanding of the process. This is due to the need for precise control over heat input, arc length, and filler metal addition. Proper preparation of the materials is also essential, including thorough cleaning to remove any contaminants that could compromise the weld. However, the time and effort invested are rewarded with welds of superior quality and durability.
Several businesses offer the services of certified and trained welders. These professionals are proficient in handling a range of materials, including aluminum, titanium, nickel, alloy steel, and stainless steel. With the approvals to work on the materials listed earlier, they are capable of providing quality weldments for a wide range of projects, from industrial fabrication to repair work. In order to provide the best services, companies should adhere to standards such as ASME Boiler and Pressure Vessel Code Section IX.

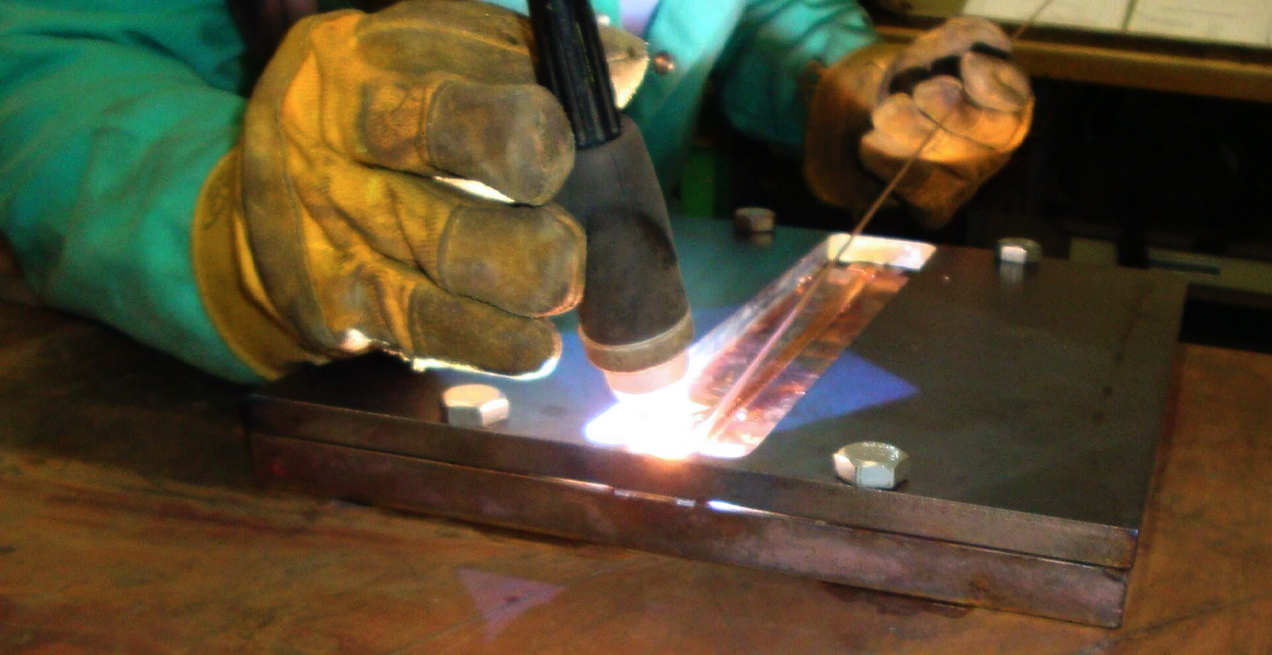
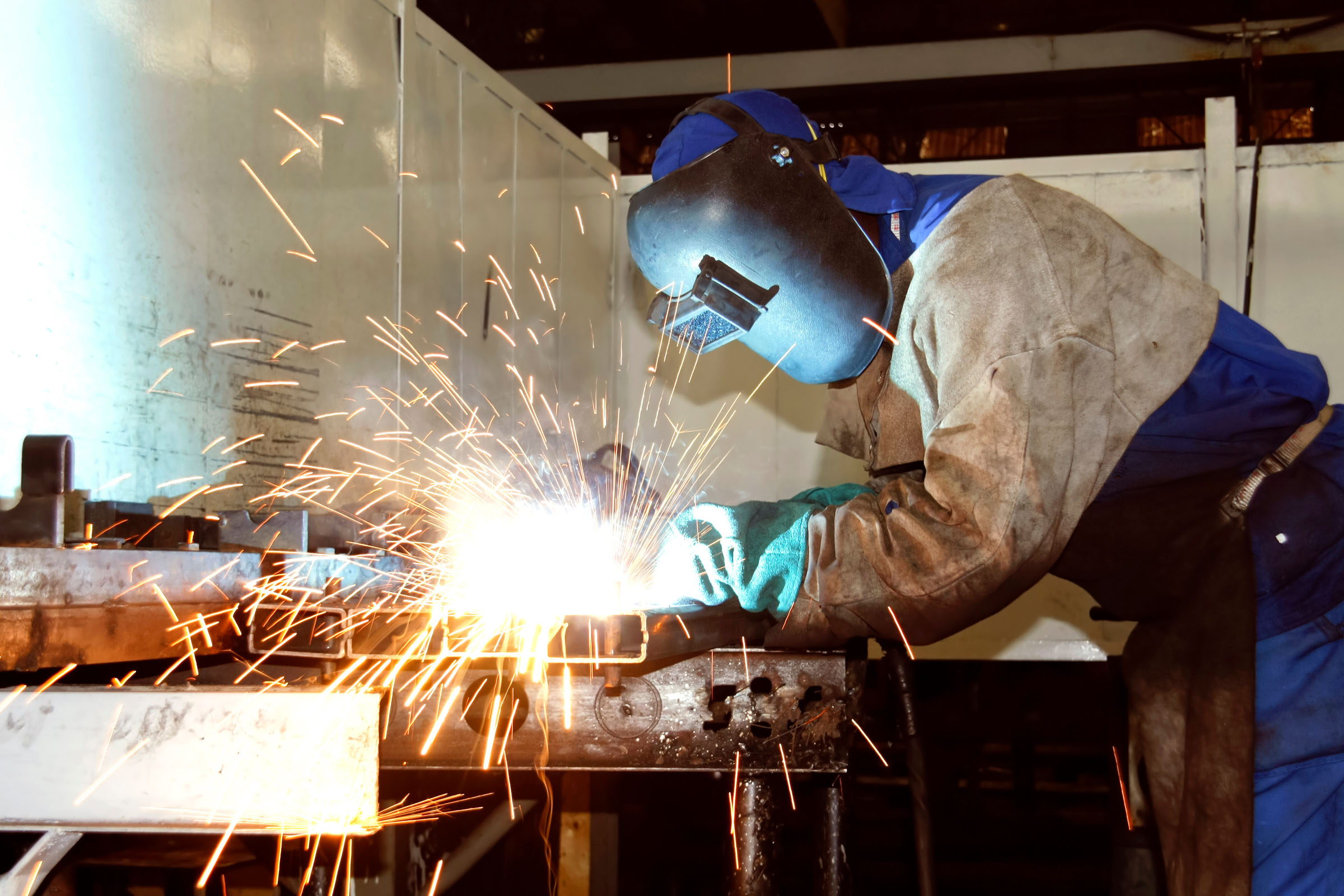